Unlocking Process Improvement Secrets: Lean and Results-Driven Solutions
- Justin Honeycutt
- Jun 13
- 1 min read
Every organization has untapped potential—time lost to inefficiency, profits slipping through process cracks, and frustrated teams stuck in outdated workflows. The solution? Strategic, lean-driven process improvement.
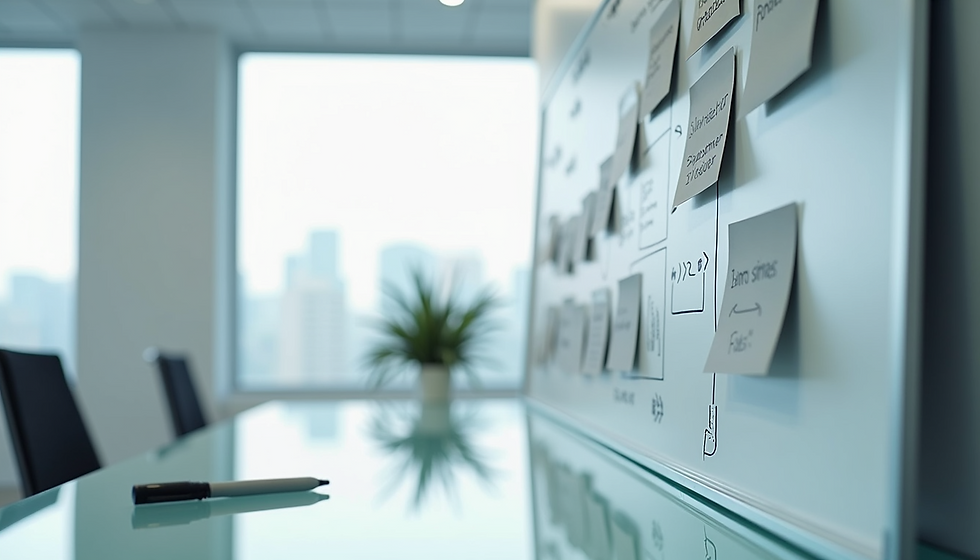
Here’s how we unlock it:
1. Start with the Value Stream
Don’t just fix symptoms—follow the value. Map out how workflows from start to finish, and you'll often find bottlenecks, duplication, and waste hiding in plain sight. Lean thinking starts with asking, “Does this add value for the customer?” If not, it's time to optimize.
2. Empower the People Doing the Work
Process improvement isn’t top-down. It’s front-line forward. Engage the individuals closest to the task—they know where inefficiencies live and often have the best ideas to eliminate them. When you involve your team, you build ownership and better solutions.
3. Small Wins. Big Impact.
Forget boiling the ocean. Identify quick wins—manual steps that can be automated, approval loops that can be simplified, or reports no one reads. These small changes create momentum and measurable impact fast.
4. Standardize, Then Improve Again
Once a better process is in place, lock it in. Document, train, and standardize. Then—reassess. Continuous improvement means the process never stops evolving.
5. Let Data Guide, Not Decide
Metrics matter, but insight wins. Go beyond dashboards. Look at trends, talk to users, and observe operations. Pair hard data with human context to make smarter, sustainable changes.
Comments